May it be to achieve food security while reducing pollution and emissions related to transportation; or to cultivate the most powerful and clean medical cannabis possible, the practice of high pressure aeroponics offers the solution. To succeed, one must know how to master the quality of the mist first, then overcome the obstacles related to its development by making the technique free for all.
The benefits of aeroponics have been known for several decades but with the recent legalization of cannabis, we are looking again for the winning formula promised by this high-level no-soil technique. However, it is rather with the vision of feeding populations more effectively that it has been experienced for 100 years.
It is also the food and ecological challenges of our time that pushed us to put this technique into practice three years ago. Like many researchers before us, we have achieved impressive results in crop health, quality and productivity while reducing the use of water and fertilizer and completely eliminating the use of phytosanitary products. But the question quickly became: Why is this technique not more used in the world of agriculture today?
Overcoming several technical challenges, such as the clogging of misters, we found that some technical limitations may have hindered the large-scale application of aeroponics. But by hovering its complex past, we saw the socio-economic factors and business confusions that prevent it from taking off and becoming a viable solution for producers and the environment.
In Quebec, where we locally produce less than 20% of our fruits and vegetables and the use of pesticides is considered the greatest threat to our waterways, it is high time we share our progress and hope that these will help make aeroponics accessible to all.
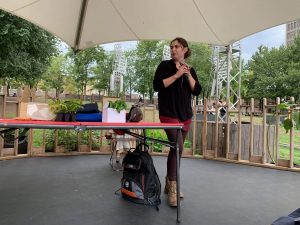
This expose of our practice in high pressure aeroponics was first presented on September 10, 2019 at Jardin Gamelin in Montreal.
Download the summary sheet here
Topics covered :
1. The aeroponic solution
” According to AgriHouse, growers choosing to employ the aeroponics method can reduce water usage by 98 percent, fertilizer usage by 60 percent, and pesticide usage by 100 percent, all while maximizing their crop yields by 45 to 75 percent. […] These results essentially proved that aeroponically grown plants uptake more minerals and vitamins compared to other growing techniques ” – NASA Spinoff (2006)
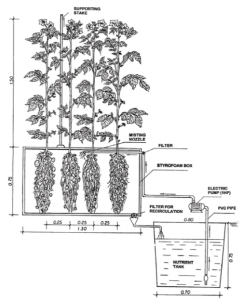
” [The University of] Ho Chi Minh has successfully studied the aeroponic method of growing broccoli, tomatoes, potatoes, spinach, etc. The results obtained were at least twice as high as those of a normal planting and cultivation on the soil … Growth 2.5 times faster; save more than 70% on irrigation ” – Trung (2011)
” Aeroponics is a soilless method for producing pre basic potato seed. The method can produce higher yields (up to 10-times higher), more quickly, and at lesser cost than conventional growing methods ” – Otazú (2010)
Although there is still a lot of research to be done on aeroponics, its effectiveness and results are no longer to be proven. NASA studies on the subject in the 80s and 90s concluded that it was the most optimal culture technique to support all forms of plants; be it for the propagation of cuttings, high-value crops or even fruit trees. Several countries such as China, Vietnam, Russia and Peru have increased their potato production thanks to aeroponics.
Performances explanation :
• Ease of nutrients uptake
• Rich in oxygen
• CO2 available to the roots
• Full health and natural defenses
The figures of Richard Stoner and NASA are impressive: 98% less water, 60% less fertilizer, 100% less pesticides (this also applies to herbicides and algicides) for 45 to 75% more production than modern conventional agriculture. This is a perfect solution for growers facing soil depletion and contamination, water shortages and phytosanitary addiction. This is even more an option to increase yields in agriculture while decreasing the pressure on territories.
Too good to be true? The explanation is simple: when you give a plant the optimal conditions by feeding it at will without forcing it, it is more productive, healthier and naturally resistant to diseases and pests. The plant does not spend all its energy building a huge root system because the nutrients are available and directly assimilated to the roots. Oxygen and CO2 are also abundant at the root level, which prevents fungal diseases and helps growth. Also, with a mist of quality, the roots are stable so there is no damage related to stress or overproduction of roots due to bad anchoring.
2. Our experimental approach in practice
In 2017, after 19 years of hydroponics experience, Jean-François crossed the frontier he had long been contemplating: putting aeroponics into practice to grow fruits and vegetables all year long. Initially, we found that there was very little material and information available, and that experienced people were not only rare but long abandoned after a few failures. However, we persisted and discovered a unique world that we never want to do without anymore.
Objective : Make a functional concept for producers by reducing equipment costs and systems maintenance without compromising performance.
With limited resources, we went in search of the perfect mist from 50 to 70 microns, the ideal filtration system at 0 micron and the root chamber with optimal height. We are not from any research centers or universities. Our approach is practical at first and experimental by default because it seemed everything had to be done to realize this concept. We much prefer to work with the best fertilizers from Advanced Nutrients but have never received sponsorship and are not affiliated with any company. We have never received grants or investments either.
The only person we were originally accountable to was our 2-year-old daughter. Our wish was to feed her pesticides-free strawberries and food security for her generation’s future. In the face of our successes, we now want to push the concept further to make this technique accessible to all producers by reducing equipment costs and systems maintenance without compromising performance.
3. Limitations and challenges of large scale application
For 30 years, we have heard the same arguments about the technical limitations of aeroponics: maintenance, cost and availability of equipments as well the reliance on electricity and the learning curve. Yet many large-scale projects have sprung up around the world and even in some countries where resources are limited.
This led us to also observe the socio-economic factors that slowed down its development. In addition to the countries that kept secret military researches in a cold-war context, we’re also facing the agroindustrial giants selling fertilizers and chemicals, for whom aeroponics is a threat to their turnover.
Technical aspects:
• Maintenance and nozzles’ clogging
• Cost and availability of equipments
• Reliance on electricity
• Learning curveSocio-economic aspects:
• Monopoly of fertilizer and phytosanitary companies
• Non qualification of no soil farming for organic certification
• Secret and military developments
To come back to the technical aspects, if the dependence on electricity and the learning curve are easily surmountable, the challenge of nozzles’ clogging is the one that posed the most problem. To obtain an ideal nutrient mist, around 50 microns according to NASA, the opening of the misting nozzle must be at its finest. In irrigation, such nozzles are used to control humidity levels and with pure water there is usually no problem. However, when we add 350 or even 500 ppm of minerals and / or organic nutrients we face a problem of clogging within 2 months sometimes even 2 weeks if there is organic matter in the solution.
Traditionally in the world of aeroponics, two strategies have been used to deal with this problem. For a university or military research center with big budgets, regularly replacing the nozzles is not a problem. However for a commercial producer, this is simply not an option considering that each mister costs between $5 and $15. Also, a need for maintenance in the middle of a season can be complicated or even catastrophic.
The other option is to widen the nozzle opening and work with low pressure systems. It lowers the costs considerably but instead of a well atomized mist we end up with a jet on the roots. This greatly reduces the benefits of aeroponics because the roots are in constant motion so stressed out, cut and overproductive.
High pressure aeroponics can also be damaging to the roots if there are pressure variations as the foggers turn on and the lines empty air in a jerky motion. We call this phenomenon “spitting on the roots”. To prevent this, the current technique consists in putting all irrigation lines under constant pressure using a pressure storage tank and several switches, electronic valves, relays and controllers. This is another expensive solution, especially since these valves often lose their effectiveness over time, which discourages many producers from adopting aeroponics.
It is hard to believe that a method more adapted to the needs of the producers had never been developed. We know that the fertilizer, pesticide, herbicide, fungicide, and algaecide industry has a lot to lose in an agrifood economy based on less polluting methods. Their lobbies have long been a drag on organic farming and aeroponics has the potential to be much more effective than organics in reducing inputs and increasing production. Today, organic agriculture is presented as the solution of the future, but 116 phytosanitary products are now allowed in organic farming and most organic fertilizer companies have either been bought by industry giants or are forced to buy their basic nutrients from the same giants.
On the other hand, as no-soil crops are not yet eligible for organic certification, producers do not have the motivation of added value to their products in order to develop them. In addition, the only commercially adopted hydroponic methods (NFT, DWC, Aquaponics) are quite greedy in water and fertilizer. A fact that does not mean anything in itself but put in context brings some lines of thought. An overview of the history of aeroponics helps put things in perspective.
4. Background and perspective of early aeroponics
First researches
Russian biologist Vladimir M. Artsikhovsky first studied bare-rooted plants and published the article “ On air plants ” in Experimental Agronomy in 1911. Several scientists in the 20th century then used this method to advance their research on root diseases such as WA Carter, who published “A method of growing plants in water vapor to facilitate examination of roots” in Phytopathology in 1942; L. Klotz, who studied the roots of sick citrus and avocado trees spayed with a mist in 1944 and concluded that the method allows for healthier trees; and G. F. Trowel, who cultivated apple trees with root jets in 1952. The Dutch botanist Frits Warmolt Went named the method “Aeroponics” with which he cultivated coffee and tomatoes in 1957.
Developments during the cold war
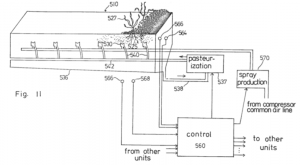
The patents filed subsequently give a clue to the early commercial developments and it can be seen that aeroponics was also at the heart of the Cold War technological race.
In Israel in 1977, Isaac Nir patented the first complete system and method using compressed air for mist, styrofoam panels and pasteurization.
Some patents were signed by the Soviet Union in the early 1980s and mainly concern foggers but there is little information in English about them.
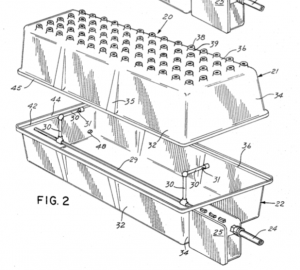
In the United States in 1983, Agrihouse (Steven Schorr and Richard Stoner) with the support of NASA patented the Genesis Machine , a device for cuttings with the first processor for automation and intermittent irrigation. In 1989, Quebec’s Karl F. Ehrlich patented a vertical design that improved the A-frame model.
In 1990, the All-Russian Research Institute of Agricultural Biotechnology (Moscow, RSFSR) began research on the use of aeroponics for reproduction of healthy virus-free seed potatoes. In 2000, a Candidate of Biological Sciences Yuri Tsaturovich Martirosyan for the first time developed the Universal Harvesting Plant “Urozhay-9000” for accelerated reproduction of healthy seed potatoes and other crops.
Meanwhile, China improved its potato tuber productivity from 11 tons / ha in 1991 to 17 tons / ha in 2000 thanks to aeroponics. In Spain, Italy and Korea several patents were also filed.
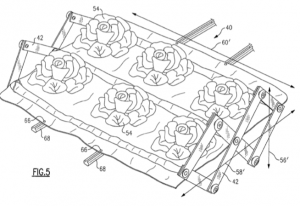
From 2006 and onward, the United States and NASA have run potato seed projects in Vietnam and Peru and are publishing their studies for the general public. The technology becomes known and the projects are multiplying in the world. Today, high-level aeroponics can be found in Ukraine, India, Japan and several African countries. The largest commercial farm is Aerofarms in New Jersey and its creators, Ed Harwood and Travis Martin, patented an aeroponic culture technology with jets and reusable fabric in 2014.
5. Business confusion
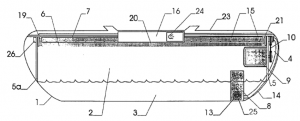
To add to the challenges that aeroponics must overcome in the popular mind, it must be mentioned that there is confusion in the market about the word itself. AeroGrow a company of Scotts-Miracle Gro affiliated with General Hydroponic and Monsanto / Bayer is the first to have marketed in 2004 a misuse of the term “Aeroponie” with its Aerogarden. In this device, the nutrient solution is at the bottom and the atomization is done by a vibrating air pump. The roots are quick to dive into the solution because the root chamber is shallow and they do not have access to a real aeroponic haze. It is actually a somewhat glorified DWC (Deep Water Culture) system.
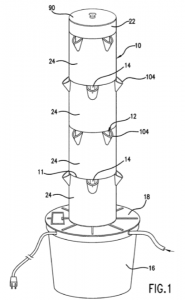
Then Tower Garden in 2006 started using the term while its system is more a vertical NFT. The nutrient solution is injected through the top of the tower and trickles inside. Interestingly, their patent does not mention the term “aeroponics” but rather “hydroponic system”. On the other hand, their marketing is based on this word and for many people their product is the very definition of aeroponics.
In both cases, these models are simple to use and functional for individuals. However their performance does not compare to high pressure aeroponics and their use requires much more water and nutrients. They are therefore ineffective models for commercial application on a large scale.
Another technique called Dry Fog is sometimes marketed as a simpler, more reliable and more economical aeroponics. In order to atomize the nutritive solution, an ultrasonic machine is used, thus eliminating the nozzles. The fog which emerges therefrom has droplet sizes between 1 and 10 microns. NASA has already determined that the ideal droplet size is 50 microns to support long-term crops. In addition, it has often been shown that Dry Fog remains suspended in the air for too long, does not collide enough with the roots and eventually takes the place of oxygen in the culture chamber. The plants develop surprisingly fast at first, but soon find themselves dehydrated, nutrient deficient and suffocated.
6. Our results and vision
For our part, we have developed different solutions to the recurring problems of aeroponics while reducing the cost of equipment and without compromising on the quality of the mist. By using a filtration system and misters more suited to our needs, we were able to eliminate electronic valve equipments and the pressure tank. Our nozzles and filters do not need maintenance during at least 8 months even with organic fertilizers and when they do they are quickly rinsed and are reusable. This allows for complete seasons without worrying about the clogging of the misters.
With a pressure of 60 to 125 psi an atomization of 50 to 70 microns is obtained. The mist is delicate but assimilable and the roots remain perfectly stable even at the opening of the irrigation lines. In addition, the gravity quickly returns the droplets to the drainage which accelerates the drying and increases the oxygen levels in the chamber. Our pumps consume very little energy and can be supported by an emergency system consisting of solar panels or chargers and 12V batteries. We still chose to put a small cube of coconut around the most sensitive part of our plants which keeps their heart moist. This allows us to have a buffer of at least 4 hours before having to irrigate in case of technical problems, lack of electricity or maintenance.
Our results speak for themselves. We harvested multitudes of strawberries, cucumbers and peppers in the middle of winter, 184 g radishes, 200 g beets, wild blackberries with 17-foot-tall branches, hundreds of Espelette peppers on each plant, lettuce larger than our children, tobacco in 3 weeks and half a kilo Aji Charapita peppers on a plant of 17 months and her two cuttings. The three Charapita are now more than 7 feet tall and 20 feet square without showing any sign of weakness or discontent with their living environment. On the contrary, we are talking about a specie that remains a 3-foot bush in its natural state in Peru. All our crops have been documented and published online to remove any doubts.
Comparing our method to that of Agrihouse called True HPAtm our benefits are in terms of maintenance and costs. Agrihouse’s systems, although they are the pioneers of the market, are still selling at astronomical prices as if they were made for space exploration budgets. The self-made HPA systems (DIY) currently found online are very similar to those at Agrihouse, at a much more reasonable cost, but still rely on electronic valves and the pressure build-up tank. We also find the same problems of clogging and if the mist is poorly calibrated we can quickly lose performance. Finally, compared to other cheap methods, our equipment is competitive but offers the true potential for high pressure aeroponic performance and efficiency.
Mist | Roots | Buffer | Maintenance | Results | Cost | |
Vertiponic | 50-70 μm √ |
Stables √ |
Heart (4h) √ |
8 months √ |
High √ |
Good √ |
True HPAtm | 20-50 μm √ |
Stables √ |
No χ |
2 months χ |
High √ |
Bad χ |
HPA DIY | 20-70 μm √ |
Average ∼ |
No χ |
2 months χ |
High √ |
Average ∼ |
Low pressure | Drops χ |
Unstables χ |
DWC ∼ |
? | Average ∼ |
Good √ |
Dry Fog | 1-10 μm χ |
Suffocated χ |
No χ |
? | No χ |
Good √ |
*** All these data are estimated according to free access information for informational purposes only.
From the beginning, we worked as a team and made a lot of sacrifices to make these projects a reality. I had to do a lot of research on vegetable crops and travel around the province and the Internet to find the right equipment. But it was Jean-François who unlocked the dead-end in which aeroponics was. Armed with his experiences in horticulture, hydroponics, mechanics and construction, he saw solutions differently where companies have spent years looking for the right path.
Tips for Winter Aeroponic Culture
Until we prepare our winter crops and open-source technology, here are some tips if you’re planning your own indoor space.
First, the choice of space requires different parameters. For a completely closed culture you must cover your walls, floors and ceiling with black & white polyethylene or silver Mylar paper to maximize your lighting and avoid mildew and other problems. Jean-François likes to build a wooden frame to minimize the holes in the walls, but there are also already silvered culture tents.
As light, we recommend a digital ballast equipped with a cooltube, blower, an HPS bulb 600W or 1000W (for flowering) and Metal Halide (for growth). Make sure that the digital ballast can fit all the bulbs you will need. The cooltube and blower are there to avoid overheating the grow room while redirecting this heat to the living space and thus save on the heating bill. With an installation as such you can add a charcoal filter if you grow cannabis and/or if you have pollen allergies.
Another option is to install the system in front of south-facing windows and add extra lighting, either Sunblaster T-5 or Sunblaster LED to extend the photoperiod. In this case make sure that all your components: pipes, tables and tanks are covered in white like polyethylene “Black & White” because the sun even in winter can overheat your nutrient solution very shortly.
For the aeroponic system you need: Pump, Filters, Misters, Roots Chamber, Tank, Plumbing, Drains, Plant Stand (3.5″ basket with clay balls and coconut or rockwool cube or neoprene), Sort period Cycle Timer (minimum 1 or 5 seconds on), Fertilizer (recommended Advanced Nutrients). Contact us for our self-assembly kits (DIY) of our technology already available including a pump, a filtration system and misters. For all hydroponic projects, you will also need some practical and essential tools: Reverse Osmosis, Computer and PH Probe, EC/PPM Pencil.
Thank you for having accompanied us so far in this presentation which is only the beginning. Jean-François reminds you that: “you have no right to make mistakes with your high value crops”. See you soon with your hands in the water and the roots in the air!
To stay in touch : Facebook group Aéroponie et Hydroponie (In French but English content most welcomed).
- Bryan, III. « Hydroponic Plant Cultivating Apparatus » Patent 7,055.282 B2. 6 Juin, 2006
- Chanh Trung / Cultiver des légumes sans sol / 2011
- Ehrlich, Karl F. « Aeroponic Apparatus » Patent 4,869,019. 26 Septembre, 1989
- NASA Spinoff (2006) Progressive Plant Growing Has Business Blooming.Environmental and Agricultural Resources NASA Spinoff 2006, pp68-72.
- Nir, Isaac. « Apparatus and method for plant growth in Aeroponic conditions » Patent 4,332,105. 1 June 1982.
- Otazú, V. 2010. Manual on quality seed potato production using aeroponics. International Potato Center (CIP), Lima, Peru. 44 p.
- Schorr, Steven et al. « Method and apparatus for aeroponic propagation of plants » Patent 4,514,930. 7 May, 1985
- Wainwright et al. « Low Pressure Aeroponic Growing Apparatus » Patent 6,807,770B2. 26 Octobre, 2004